1、超声波检验方法的特点及适用范围
无损检验方法包括射线检验、超声波检验、磁粉检验和液体渗透检验几种方法。磁粉检验和液体渗透检验主要用于检验表面和近表面的缺陷显示。射线检验和超声波检验主要用于检验锻件内部的缺陷。射线检验主要用于检验本身有一定高度的缺陷显示,而超声波检验主要用于检验面积型缺陷显示。
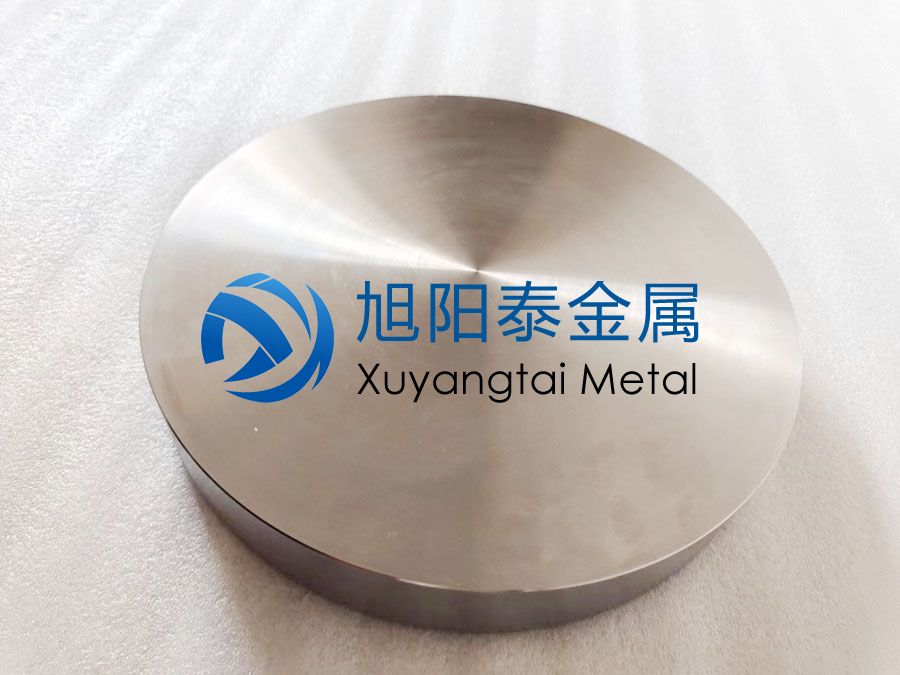
超声检测一般是指使超声波与工件相互作用,就反射、透射和散射的波进行研究,对工件进行宏观缺陷检测、几何特性测量、组织结构和力学性能变化的检测和表征。超声检验是指利用超声波对材料的质量进行评估的技术。超声检验具有穿透能力强、检验成本低、速度快、灵敏度高、缺陷定位较准、对现场环境要求低等优点,广泛应用于工业领域。
2 、锻件的加工工艺及常见缺陷
锻件是由低合金钢在热态下,通过压力加工而形成。这种压力加工包括自由锻、快速锻和挤压锻等不同的锻造方式。锻造中易产生的缺陷有非金属夹杂物、裂纹、白点、偏析、重皮(白点)等。这些缺陷的主要特点为:裂纹:锻造或锻后热处理工艺操作不当,如加热过快、终锻温度太低、应变太快、太大或坯料原有缺陷,引起锻件局部破裂而形成裂纹。锻造裂纹多见于锻件表面。裂纹主要有中心锻造裂纹、内应力引起内部裂纹、缩孔残余裂纹、夹杂些裂纹等。
2.1 中心锻造裂纹
中心锻造裂纹的产生可归纳为三方面的原因:
(1)锻造前,工件加热不均匀或不足,俗称没有烧透;
(2)最终锻造温度过低,工件外部冷却快,中部冷却慢;
(3)温度过大,由于高熔点或低熔点的夹杂物在晶界上密集折出。
2.2 内应力引起内部裂纹
在高碳或高合金钢锭加热时,工件内部有时形成横向或纵向裂纹。原因是钢锭表面加热快,表面与内部温差大,表面热胀也会对内部形成较大的拉应力,即热应力。再与残余应力共同作用下,纵向拉应力也可能导致锻件内部产生横裂纹。
2.3 缩孔残余裂纹
锭模不当,浇铸不当,缩孔不完全集中在冒口,或冒口切除不足致使缩孔残余留在工件中,引发的裂纹。如果锻件所使用的钢锭有较严重的缩孔,在锻造时没有完全切除,将在锻件中形成残余缩孔裂纹缺陷。
2.4 夹杂形裂纹
夹杂物比较集中、比较严重的钢锭锻造工件时,由于夹杂物的存在也使工件破裂而形成中间有夹心的夹杂性裂纹,这种缺陷和夹杂物混杂在一起。
白点:在某些金属零件的断口上,有时会发现圆形和椭圆形,表面光滑呈银白色的斑点,尺寸大小不等。实质上,白点缺陷是裂纹性缺陷,它严重影响着金属的延伸率、收缩率及韧性,白点缺陷是由于氢和组织应力造成的,在冶炼和浇铸、锻造过程中进入金属中的氢元素是以院子形态存在的,在锻造后过程中,由于缓慢冷却,原子氢有从金属内部向外部扩散的趋势,如果冷却过快,溢不出来的氢分子,在聚集的地方会造成巨大的局部氢压力,超过金属强度就产生了白点缺陷。
容易使金属材料破裂的原因有:
(1)开始在热应力与相变应力共同作用下形成微小裂纹核;
(2)强化元素与氢的联合作用使微裂纹核扩大;
(3)氢会使材料组织应力增高、钢的晶格强度会下降;
(4)溶解的氢会向微小裂纹的自由表面扩散,促使应力升高,或产生氢脆使裂纹产生不稳定的状态,所以白点类缺陷的形成过程,是一个逐渐发生和不断长大的过程。
白点类缺陷较为集中,对超声波的漫反射衰减很严重,影响底面反射波高度及底面反射次数。
折叠:锻造时操作不当,锻件表面凸出部位或氧化皮挤压在锻件中形成折叠。折叠位于锻件表面或近表面,又称重皮。
夹杂:冶炼、浇铸时,残留在金属中的难熔金属或非金属杂质形成片状夹杂。
3、 锻件超声波检验方法及控制要点概述
超声波检验是上述缺陷检验的主要检验方法。由于制造稳压器的锻件的几何形状和结构不同,所采用的超声检验技术也不同,但最终的目的都是要反映出工件的内部质量状况,保证所制造的产品满足标准要求。在稳压器项目制造过程中合金钢锻件和不锈钢锻件的超声波检验主要依据 RCC-M (2007 版)及 FM1061修改单进行超声波检验,进行超声波检验的锻件见表 1。
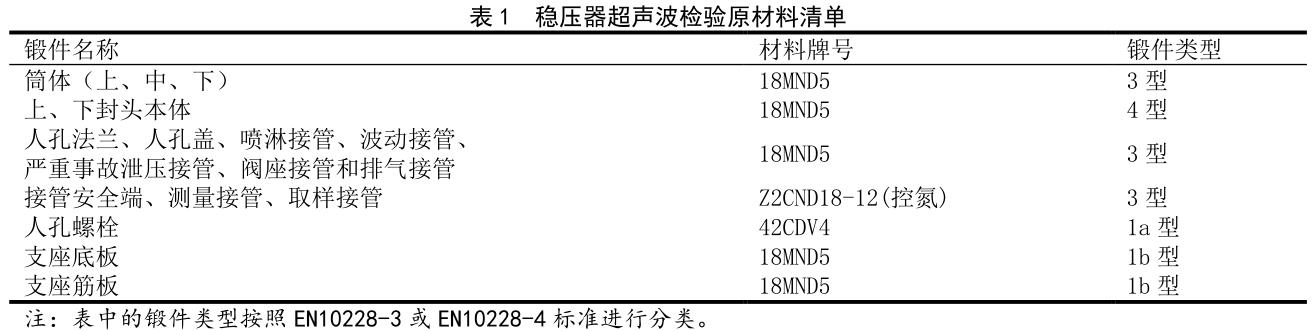
从表 1 可以看出,锻件类型主要包括 1 类、3 类和4 类。现分别对不同类型的锻件的超声波检验方法及控制要点进行概述:
3.1 1 型锻件
1 型锻件分为 1a 型和 1b 型,1a 型锻件为圆柱形锻件,1b 型锻件为矩形锻件。
1 型锻件的锻造工艺主要以拔长为主,因而大部分缺陷的取向与轴线平行。因此,超声波检验时以纵波直探头检测效果最佳。超声波检验时,1b 型应从图示1 中的两个相互垂直的表面及纵向表面即共三个面进行检验,检验方案制定需注意锻件检验时对比试块的选择是否满足被检工件厚度要求。1a 类圆柱形锻件进行超声波检验时不仅需按图示进行环绕圆柱侧面进行100%扫查,同时还应用直射纵波在锻件的端面作轴向检验,在检验方案制定的过程中通常存在下述问题:
3.1.1 工件直径小耦合不好
人孔螺栓为 M48×527mm 的棒材,棒材锻件类型为1a 类,按设计文件要求应在棒材圆周面和端面对棒材进行 100%的超声波检验。棒材直径较小,此时若选择单晶直探头晶片尺寸较大,则探头与被检工件的间隙较大,耦合效果差,此时为避免探头摇动并保证探头与工件良好的、均匀的声耦合,可在探头前加装曲率与被检验工件相吻合的探头靴,此时应注意校准时和检验时均应使用探头靴。
3.1.2 1a 类锻件长度过长产生侧壁干涉
对于 1a 类锻件,当纵波直探头检验时,探头若靠近侧壁,则经侧壁反射的纵波或横波与直接传播的纵波相遇产生干涉,对检验带来不利影响。为了避免产生侧壁干涉而影响检验结果的判定,在审核供方制定的无损检验方案时,应注意 1a 类锻件的长度是否会产生侧壁干涉,若产生侧壁干涉,可采用的解决方案为:
①是否可将过长产生侧壁干涉的锻件切割开后分段进行超声波检验;②当锻件长度不可分割时可在锻件圆周面增加斜探头轴向检验进行补充。
3.1.3 试块中反射体的深度与被检验工件的厚度不符合
锻件进行超声波检验时应至少使用 3 个孔来制作DAC 曲线,并且该 DAC 曲线应覆盖整个被检锻件的厚度,但有时供方无损检验方案中的试块厚度不满足要求,此时建议供方设计制造新的试块或是增加双晶直探头补充 1a 类锻件检验时产生的盲区,保证能做到对锻件的全体积进行检验。
3.2 3 类锻件
稳压器接管锻件(人孔法兰、人孔盖、喷淋接管、波动接管等)为 3 类锻件,此类锻件的锻造工艺是先镦粗,后冲孔,再滚压。因此,缺陷的取向比轴类锻件中的缺陷取向复杂,所以该类锻件的检测既需要进行纵波检测,还应进行横波斜入社检测。稳压器项目的 3类锻件主要按照 EN10228-3 或 EN10228-4 标准的规定 3类锻件外内径之比小于等于 1.6 时需要进行斜射波周向检验。
针对此要求需注意下述问题:
3.2.1 锻件工艺余量导致检验疏漏
制造厂出于制造工艺的需要对于稳压器上的接管等 3 类锻件提料时内外壁均留有余量,使得根据上游图纸最终外内径之比小于 1.6 的 3 类锻件在采购时外内径之比大于 1.6,根据标准此时不需要进行斜射波周向检验,而锻件在制造过程中机加工到最终尺寸后(外内径之比小于 1.6)又疏漏了此项检验要求,导致在漏检或在接管内壁堆焊完并焊接到封头上后进行了补充检验,此时进行超声波检验因内壁存在堆焊层并且锻件结构形式等原因导致检验效果远不如在锻件制造厂检验效果好。鉴于上面的经验反馈,在稳压器人孔法兰、喷雾接管、波动接管、严重事故泄压接管、阀座接管和排气接管等锻件采购阶段,在锻件图中标注锻件最终轮廓,并在锻件图的技术要求中规定按照锻件的最终轮廓对锻件进行斜射波超声波检验,且校准试块反射体的制作应按锻件的最终尺寸。此要求消除了锻件在原材料供方不进行超声波检验而锻件入厂进行超声波检验而不合格的风险,同时保证了锻件在
最适合的时机和形状进行了超声波检验。
3.2.2 3 类锻件斜探头检验耦合问题
对于接管及接管安全端等 3 类锻件,当外内径之比小于 1.6 时需要进行斜射波检验,当锻件外径小于250mm 时,应注意探头与工件表明的耦合情况,为避免探头摇动并保证探头与工件的良好的、均匀的声耦合和恒定的声束角度,可安装仿形的探头靴。校准时和检验时均应安装探头靴。
3.2.3 温度测量接管等接管钻孔后的斜射波检验
稳压器的取样接管等仪表接管为 3 类锻件,且外内径之比小于 1.6,应进行正反两个方向的周向斜射波检验,接管的外径为¢35mm,内径为¢23mm,壁厚为 5.5mm,材质为 Z2CND18-12(控氮)。接管锻件进行接触法超声波检验时的难点为:管径小,曲率大,入射声束从曲面入射的一开始就由于晶片的切向尺寸影响,而必然有发散,检验过程中容易有干扰波产生;而声束在管壁内传播,要经过管材内壁反射,声束发散同样较大,检验过程中波束扩散严重,灵敏度低。同样,接触法探头斜楔使用一段时间后必然会发生磨损,从而导致斜探头在工件中的折射角发生变化,将导致检验灵敏度降低。为了改善此问题,我公司设计制作水浸探头工装并定制水浸聚焦探头,使得声束在工件中得到进一步聚焦,提高了检验灵敏度,水浸聚焦探头选择及参数设置见表 2,水浸检验水套工装见图。
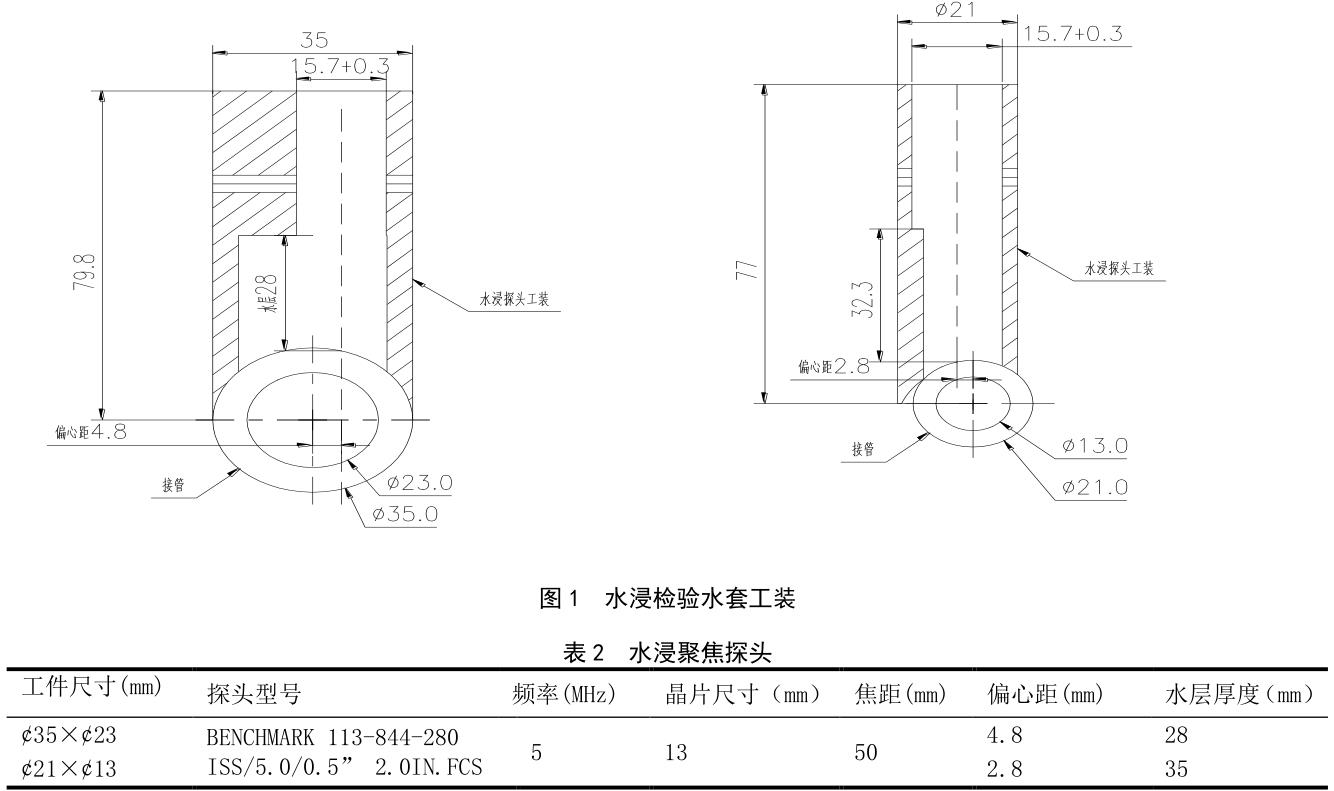
3.3 4 类锻件
4 类锻件的锻造工艺主要以镦粗为主,缺陷以平行于端面分布为主,所以用直探头在一个平面上扫查,同时采用斜射波在锻件的表面进行四个方向的检验。
4 、总结
锻件在核电产品制造过程中的应用极为广泛,而超声波检验是锻件产品质量控制的一种重要的无损检验方式。结合稳压器制造过程中锻件所用锻件的特点及在检验时存在的问题,对锻件超声波检验总结如下:
4.1 合理选择超声波检验的时机
锻件的超声波检验通常安排在调质热处理后进行,如果由于锻件的几何形状限制,不能在调质热处理之后作全面检验,允许在调质热处理前进行检验,但在调质热处理后仍需要对其再次进行尽可能完整的超声波检验。若锻件在锻造过程中,需要钻孔、开槽、车斜度或加工外部台阶轮廓,则超声波检验应安排在这些加工工序前进行。
锻件检验超声波时应关注锻件的形状及最终锻件尺寸,根据最终锻件尺寸选择超声波检验探头试块等工艺参数;当最终尺寸不能进行检验时可在接近最终尺寸的阶段进行检验,当由于锻件尺寸原因无法实施最低要求的检测时应选择合适的方案进行补充。
4.2 选择合适的超声波检验探头
超声波检验时超声波检验探头的选择至关重要,尤其是检验曲率较大的锻件,如果此时选择平面探头,则探头与被检工件的耦合较差,致使灵敏度降低,将会导致缺陷漏检。因此,在检验时对曲率较大的锻件,可选用探头与被检工件表面间隙不大于 0.5mm 的探头,可修磨探头斜楔或选择晶片尺寸较小的探头,保证耦合效果。但此时应注意斜探头角度的变化,应设计制作相应的试块对斜探头的入射角和前沿值进行测量。
4.3 试块的选择
为了避免锻件超声波检验时因试块与被检工件衰减不同或曲率不同而引起的检验结果的差异,试块的制作应按下述要求:
试块的材料应取自:
被检件延长段或被检件中割下的余料;
与被检具有相同材料和热处理状态的部件上割下的余料;
与被检件具有相近声学特性的材料,通常要求声速为被检工件的±5%;
除应关注被检工件与试块材料方面的差异外,还应注意不同曲率造成的差异,通常,被检件的检测面曲率半径小于或等于 250mm 时,应采用曲率半径与工件相同或相近的对比试块进行灵敏度的校准。
4.4 根据锻件的制造工艺选择合适的检验面
结合锻件的制造工艺等特点,锻件超声波检验在可达时在至少两个相互垂直的表面进行直射波检验,对于筒形锻件和碗形锻件还应采用斜射波进行周向斜射波检验或周向斜射波和轴向斜射波相结合的四个方向的检验。
4.5 检验过程的控制
锻件检验时,虽然有些缺陷的当量大小未达到拒收水平,但是多个小缺陷的存在会对底面回波产生影响。因此,在检验时应同时关注底波降低量和是否存在超过验收准则的不合格缺陷显示存在。
参考文献
[1]李述亭,郑国渠,黄群.钢锻件超声检测缺陷定性分析研究[J].钢铁研究学报,2013(5).
[2]康洪涛.大型锻件的超声波检测[J].重庆理工大学,2010(10).
[3]张国杰.平锻机锻件缺陷分析及对策[J].锻压装备与制造技术,2013(2).
相关链接